Jason Schuster: Difference between revisions
(→Bio) |
|||
(16 intermediate revisions by the same user not shown) | |||
Line 4: | Line 4: | ||
==Bio== | ==Bio== | ||
I grew up on a farm, and have been a DIYer, Maker, Fabricator my whole life. I attended the University of Nebraska at Lincoln and earned a Bachelor's | I grew up on a farm, and have been a DIYer, Maker, Fabricator my whole life. I attended the University of Nebraska at Lincoln and earned a Bachelor's of Science in Mechanical Engineering. I then went to industry as a Design Engineer, where I worked at Caterpillar for 5 years and Case New Holland for 7 years. In 2015, I decided to go back to school for a Master's degree. I chose the Biomedical Engineering field because I wanted to stay in engineering and learn more about the ultimate machine, Humans! My favorite activity is riding and racing bicycles, learning more about how the human body works would give me a fundamental understanding on how to improve fitness, recover faster, design better bicycles, and improve the human-bicycle interaction! | ||
<br /> | |||
'''2021 Update!''' | |||
<br /> | |||
In August 2019 I got a ticket on the Awesome Bus to work at Trek Bicycles in Waterloo, Wisconsin! Without a doubt, the coolest and most fun job I have ever had! I am in the Bontrager Essentials group and we design many of the aftermarket components such as Saddles, Grips, Pedals (all the Human Machine Interaction points), fenders, bags, pumps, and more. | |||
Once we get beyond the pandemic, if you are ever in Wisconsin and want to stop by for a tour, I would be happy to give my fellow alumni friends a persona tour! | |||
If you have questions on how to get your own dream job, please reach out by my alumni Wavemail email account listed below! | |||
I'm also not hard to find on LinkedIn if you want to connect there, just be sure to send me a message with your connection request. | |||
'''Jason Schuster''' | '''Jason Schuster''' | ||
<br /> | |||
'''Maker Ninja''' | '''Alumni Maker Ninja (Spring & Fall 2018)''' | ||
<br /> | |||
''' | '''Alumni Graduate Student (Fall 2015 - Fall 2018)''' | ||
<br /> | |||
'''Department of Biomedical Engineering''' | '''Department of Biomedical Engineering''' | ||
<br /> | |||
'''Lab Website: '''[https://sites.google.com/view/bgandrlab Biomechanics of Growth & Remodeling Lab] | '''Lab Website: '''[https://sites.google.com/view/bgandrlab Biomechanics of Growth & Remodeling Lab] | ||
<br /> | |||
'''Email:''' [mailto:jschust5@tulane.edu jschust5@tulane.edu] | '''Email:''' [mailto:jschust5@tulane.edu jschust5@tulane.edu] | ||
Line 56: | Line 57: | ||
<br /> | <br /> | ||
==Tulane Makerspace Project Portfolio== | ==Tulane Makerspace Project Portfolio== | ||
Line 66: | Line 65: | ||
<li style="display: inline-block;"> [[File:Cruciform stamp.jpeg|thumb|none|300px|Tissue Stamp - Laser Cut Acrylic on the Epilog Helix]] </li> | <li style="display: inline-block;"> [[File:Cruciform stamp.jpeg|thumb|none|300px|Tissue Stamp - Laser Cut Acrylic on the Epilog Helix]] </li> | ||
<li style="display: inline-block;"> [[File:stamp_shelf_1.JPG|thumb|none|300px|Organizer Box for the stamps, created using the Inkscape Boxmaker Extension]] </li> | <li style="display: inline-block;"> [[File:stamp_shelf_1.JPG|thumb|none|300px|Organizer Box for the stamps, created using the Inkscape Boxmaker Extension]] </li> | ||
<li style="display: inline-block;"> [[File:clamp_fixtures.JPG|thumb|none|300px| | <li style="display: inline-block;"> [[File:clamp_fixtures.JPG|thumb|none|300px|These fixtures align the tissue clamps, they are made in 1mm increments to match the variable size of tissue specimens - Designed in Solid Works and 3D Printed]] </li> | ||
<li style="display: inline-block;"> [[File:Push stick saw.JPG|thumb|none|300px|Wood 1 Push Stick]] </li> | <li style="display: inline-block;"> [[File:Push stick saw.JPG|thumb|none|300px|Wood 1 Push Stick]] </li> | ||
<li style="display: inline-block;"> [[File:Keyboard stand.JPG|thumb|none|300px|Keyboard Stand]] </li> | <li style="display: inline-block;"> [[File:Keyboard stand.JPG|thumb|none|300px|Keyboard Stand]] </li> | ||
Line 91: | Line 90: | ||
<li style="display: inline-block;"> [[File:both_stp1_done_2.JPG|thumb|none|300px|CNC Milled Maple Shoe Lasts (Step 1) see write-up below for more info]] </li> | <li style="display: inline-block;"> [[File:both_stp1_done_2.JPG|thumb|none|300px|CNC Milled Maple Shoe Lasts (Step 1) see write-up below for more info]] </li> | ||
<li style="display: inline-block;"> [[File:larger_cannula.JPG|thumb|none|300px|Larger cannula, 7mm and 8mm diameters]] </li> | <li style="display: inline-block;"> [[File:larger_cannula.JPG|thumb|none|300px|Larger cannula, 7mm and 8mm diameters]] </li> | ||
<li style="display: inline-block;"> [[File:tube_bender.JPG|thumb|none|300px| | <li style="display: inline-block;"> [[File:tube_bender.JPG|thumb|none|300px|Tube bender for the 2mm tubing part of the cannula]] </li> | ||
<li style="display: inline-block;"> [[File:hook_stand.JPG|thumb|none|300px|Fixture stand for placing the fish hooks in the tissue]] </li> | <li style="display: inline-block;"> [[File:hook_stand.JPG|thumb|none|300px|Fixture stand for placing the fish hooks in the tissue]] </li> | ||
<li style="display: inline-block;"> [[File:detail_hook_stand.JPG|thumb|none|300px|The acrylic top is laser cut on Epilog Helix laser cutter and then drilled with a countersink to make the screw flush ]] </li> | <li style="display: inline-block;"> [[File:detail_hook_stand.JPG|thumb|none|300px|The acrylic top is laser cut on Epilog Helix laser cutter and then drilled with a countersink to make the screw flush ]] </li> | ||
Line 147: | Line 146: | ||
Update: 11 Feb 2019 | Update: 11 Feb 2019 | ||
Bont Cycling has beat me to it! Check out their recent Facebook post: | |||
<li style="display: inline-block;"> [[File:Bont_wide_toe_box.JPG|thumb|none|300px|Bont Cycling Wide Toe Box Shoes!]] </li> | <li style="display: inline-block;"> [[File:Bont_wide_toe_box.JPG|thumb|none|300px|Bont Cycling Wide Toe Box Shoes!]] </li> | ||
The question for me now becomes, what do I do now? I | The question for me now becomes, what do I do now? I still have a ton of work to do to make my own shoes. Well the answer is obvious to me, I'm done making my own shoes and I will now buy a pair of Bont's instead! | ||
(I will still finish my pair of Last's, but now that I am no longer at the Makerspace, a CNC mill is much more difficult to get access too, so Bont's timing is perfect.) | |||
==Exorcist3D YouTube Channel== | ==Exorcist3D YouTube Channel== | ||
Line 202: | Line 202: | ||
==Last Updated== | ==Last Updated== | ||
6 March 2019 |
Latest revision as of 15:56, 30 January 2021
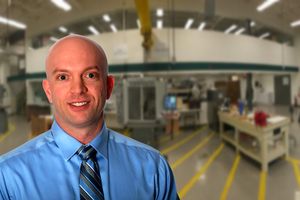
Bio
I grew up on a farm, and have been a DIYer, Maker, Fabricator my whole life. I attended the University of Nebraska at Lincoln and earned a Bachelor's of Science in Mechanical Engineering. I then went to industry as a Design Engineer, where I worked at Caterpillar for 5 years and Case New Holland for 7 years. In 2015, I decided to go back to school for a Master's degree. I chose the Biomedical Engineering field because I wanted to stay in engineering and learn more about the ultimate machine, Humans! My favorite activity is riding and racing bicycles, learning more about how the human body works would give me a fundamental understanding on how to improve fitness, recover faster, design better bicycles, and improve the human-bicycle interaction!
2021 Update!
In August 2019 I got a ticket on the Awesome Bus to work at Trek Bicycles in Waterloo, Wisconsin! Without a doubt, the coolest and most fun job I have ever had! I am in the Bontrager Essentials group and we design many of the aftermarket components such as Saddles, Grips, Pedals (all the Human Machine Interaction points), fenders, bags, pumps, and more.
Once we get beyond the pandemic, if you are ever in Wisconsin and want to stop by for a tour, I would be happy to give my fellow alumni friends a persona tour!
If you have questions on how to get your own dream job, please reach out by my alumni Wavemail email account listed below!
I'm also not hard to find on LinkedIn if you want to connect there, just be sure to send me a message with your connection request.
Jason Schuster
Alumni Maker Ninja (Spring & Fall 2018)
Alumni Graduate Student (Fall 2015 - Fall 2018)
Department of Biomedical Engineering
Lab Website: Biomechanics of Growth & Remodeling Lab
Email: jschust5@tulane.edu
Maker Skills:
- 3d Printing: Laser Cutter, Lathe, Mill, Woodworking, Sand casting
- Welding: TIG, MIG, Stick, & Oxy-acetylene
- CAD: Solidworks, AutoDesk Fusion 360, Pro/Engineer CREO, Geomagic/Cubify Design
- CAM: AutoDesk Fusion 360, Inventables Easel
- 3D Printing: Cura, Sprinter Firmware, Slic3r,
- Graphics: Inkscape, Adobe Illustrator, Adobe Photoshop, GIMP
- Programming: LabVIEW, MATLAB, Mathematica
- Makerspace Training Certifications:
Tulane Makerspace Project Portfolio
-
Made on the Carvey - 2 Color HDPE -
Tissue Stamp - CNC Milled Precision Stamping Fixture -
Tissue Stamp - CNC Milled Precision Stamping Fixture -
Tissue Stamp - Laser Cut Acrylic on the Epilog Helix -
Organizer Box for the stamps, created using the Inkscape Boxmaker Extension -
These fixtures align the tissue clamps, they are made in 1mm increments to match the variable size of tissue specimens - Designed in Solid Works and 3D Printed -
Wood 1 Push Stick -
Keyboard Stand -
Keyboard Stand Detail -
Dogbone stamp for mouse patellar tendon. Thats 0.75mm between the blades! Laser cut on the Epilog Helix, acrylic -
Keyence laser caliper and Thorlabs fixture -
Surface plate for laser caliper - Made on the Tormach PCNC 770 Mill -
Unconfined compression plattens - Made on the Tormach PCNC 770 Lathe -
cutting mats for tissue stamps - Made on the Carvey -
completed cannula assembly with simple tube benders -
I helped with the design work for this device, here's how the cannula are used -
Added the hex to these previously made canula parts - Made on the Tormach CNC Mill -
Top and bottom biochamber brackets, I added the shallow large diameter countersink to each part. A collar fits into the countersink and will align the test fixtures mounts - Made on the Tormach CNC Mill -
Simple Locker Shelves design - Laser Cut -
Shelves installed in my locker -
CAM programming Fusion360 -Planar biaxial balancing grip -
I made the 4mm diameter PTFE (teflon) roller on the lathe, the aluminum plate is the exact thickness to use a razor blade to make the final cut. -
After cutting the gripping stock off, the roller is left with the desired height -
Designed in Solid Works, CAM programming in Fusion360 - This is a double roller assembly to balance the tension in 4 sutures used to pull on soft tissue in a planar biaxial configuration. -
Jig for making 100mm spaced fish hook grips for the planar biaxial device, These are used with the double rocker assemblies. Designed in Solid Works, Laser cut acrylic, and for fun, I used the media blaster to "fog" the bottom of the part -
CNC Milled Aluminum Tendon Stamp, the width between the razor blades is 0.75mm! -
Compression Platten for the lab, Hex nut pocket milled by CNC -
CNC Milled Maple Shoe Lasts (Step 1) see write-up below for more info -
CNC Milled Maple Shoe Lasts (Step 1) see write-up below for more info -
Larger cannula, 7mm and 8mm diameters -
Tube bender for the 2mm tubing part of the cannula -
Fixture stand for placing the fish hooks in the tissue -
The acrylic top is laser cut on Epilog Helix laser cutter and then drilled with a countersink to make the screw flush
Wood 1 Saw Handle Push Stick Pattern
If you would like to make a saw handle push stick for fun or for your Wood 1 training, here's the file! I laser engraved this pattern onto the piece of wood and then brought that to class, however, you could alternatively use the OLD SCHOOL CUT AND PASTE method! Yes, you guessed it: print the handle onto paper, cut it out with scissors, and then trace the design onto the wood. Not as technically cool, I know, but you will still end up with an awesome saw handle push stick (which could be engraved later!). Click on the image below and follow the "original file" link to download the PDF.
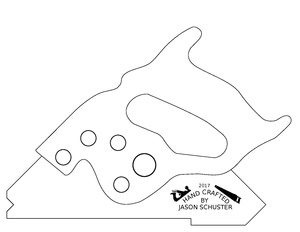
Custom Cycling Shoes Project
This year (January 2018) I have decided to start a long term project to make my own custom footwear! Shoe styles the world over are driven by elegant form NOT function! You know what I'm talking about; the extreme examples are narrow or pointed dress shoes! I don't know anyone with a foot that narrow and toes forming a pointy triangle... There is a new wave of shoe companies now making wide toe box shoes, which are actually shaped like your foot. Running and daily shoes are available (e.g. Altra Running Shoes), however no one is yet making a cycling shoe. Cycling shoe companies are notorious for making super narrow shoes. It is possible to buy custom made shoes (e.g. Rocket7 Cycling Shoes), Rocket7 makes some awesome shoes, but the custom work also has a custom price. I think I can Do-It-Myself for a fraction of the cost and it will be fun!
I am going to mix new technology with the old, however, most of this project will require learning an old world artisan skill, which is something I enjoy doing. I am going to document the journey here.
- STEP 1: Create a 3D CAD model of my feet. The Tulane Makerspace has an iSense 3D scanner, Here are images of the test scans I did for a proof of concept.
UPDATE: This is not a Makerspace Tool, but I was lucky enough to get access to a Creoform Go! 3D Scanner.
- STEP 2: After completion of the 3D models, I will next be creating a "last" this is the foot form that shoes are built on. Maple hardwood is the best material to use for a last. I am planning to use the Tormach CNC Mill to transform the 3D model into a wooden last shaped just like my foot.
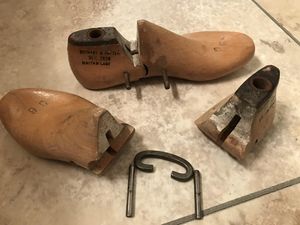
A great advantage of having a custom pair of lasts is they can be used to make almost any type of shoe. If I figure all this out, I hope to someday make my own custom leather dress shoes from these lasts! Worst case, if I can make them, then I could send them to someone else that can!
UPDATE 17 DEC 2018: CNC Milling the maple blocks. Here's the work in progress:
So that's as far as I will get at the Tulane Makerspace. This first step of milling is the last thing I had on my list before heading out. I finished up my Master's degree this semester and have decided to not pursue the PhD any further. So on to the next chapter in life! I do plan to continue working on this project and I'll post updates when I do.
Once I finish up the milling of the last here's a summary of the next steps:
- STEP 3: Create the patterns - There are a lot of videos on youtube for how to do this.
- STEP 4: Materials - I have been scavenging eBay looking for old cycling shoes I can cut up and use the hardware from. Figuring out where to buy synthetic leather, foam, and fabrics is going to take some time and research. Finding materials may actually be one of the hardest parts of this project.
- STEP 5: Hand Tools: The best tools look to be made by CS Osborne, there's a few specialty tools I'll be needing. I already own the primary and most expensive tool for this project, which is a heavy duty walking foot sewing machine.
- STEP 6: The Sole - Originally, I was planning to do a carbon fiber layup, but after investigating it, I think I will start with fiberglass & resin, I think it will be a much simpler plan since I already have some experience with these materials.
Update: 11 Feb 2019 Bont Cycling has beat me to it! Check out their recent Facebook post:
The question for me now becomes, what do I do now? I still have a ton of work to do to make my own shoes. Well the answer is obvious to me, I'm done making my own shoes and I will now buy a pair of Bont's instead! (I will still finish my pair of Last's, but now that I am no longer at the Makerspace, a CNC mill is much more difficult to get access too, so Bont's timing is perfect.)
Exorcist3D YouTube Channel
Here's my YouTube channel, several videos of my 3D printer and South Bend lathe are found here:
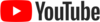
OpenSource 3D Printer
In 2013, I built my own opensource 3D Printer. I modified the Prusa i3 design. Controlled by: Arduino Mega + RAMPS 1.5 with Sprinter firmware. The frame is made from 1/4" laser cut steel plates and 3/4" lathe turned rods. The build surface is heated and has a 10" x 10" x 10" build volume. Recently, I made several improvements and upgrades, which include a large screen LCD with SD card reader, X-axis belt tensioner, print cooler fan, and a genuine E3D Titan Extruder, which I mounted Bowden style (filament drive is remote mounted like the Ultimaker configuration). Many of these upgrades were printed in the Makerspace! Detailed list below. Future upgrades include a BL Touch auto bed level and 1.75mm genuine E3D V6 Nozzle.
Several of the parts I printed in the Makerspace: * Tan LCD display box * Purple X-axis belt tension bracket * Purple Arduino & Ramps box * Purple Printer cooler fan shroud
If you are interested in building your own open source 3D printer, I suggest starting here: Reprap.org Also, the Lulzbot Taz machines are open source, all files to build their machine is available on their webpage! Same for the new Prusa printer recently added to the lineup.
1934 South Bend Lathe & Projects
This South Bend lathe is my own personal lathe, located in Nebraska. In 2010, I restored this lathe back to working condition. Over Christmas break (2017), I machined some small parts for my lab. These parts are cannula, used to mount soft tissues in our TA Instruments inflation-extension test device. The material is PEEK plastic, it can withstand the temperature of an autoclave, and machines nicely. Check out my YouTube link above, there is a quick video of the PEEK being machined.
Last Updated
6 March 2019